О строительстве традиционном и не очень.
Цемент из местного сырья
Публикуя статью Я. В. Смирнова, редакция надеется, что молодежь известковых и кирпичных - заводов проявит инициативу в практическом осуществлении его предложения и своим опытом получения цемента из местного сырья по упрощенной технологии поделится на страницах нашего журнала.
Иван Васильевич СМИРНОВ — один из старейших советских изобретателей в области промышленности строительных материалов. Особенно широкую
известность он получил в связи с открытием им способа так называемого гидратационного твердения извести. За эту работу в 1949 году внеочередным постановлением ему была присуждена Сталинская премия первой степени.
В настоящее время И. В. Смирнов
работает в Научно-исследовательском
институте новых строительных материалов Академии строительства и архитектуры СССР.
ВОЗНИКНОВЕНИЕ ПРОБЛЕМЫ
Цемент — это «хлеб» строительной индустрии. Сейчас, пожалуй, нет ни одного мало-мальски крупного строительства, где не применялся бы этот вяжущий материал. Наиболее же широкое распространение он получил в связи с развитием индустриальных методов производства строительных работ из сборного железобетона.
Однако, несмотря на огромные достижения современной науки в области производства цемента и небывалое развитие цементной промышленности, нашим многочисленным стройкам все еще не хватает этого «хлеба». Особенно большой цементный голод ощущают стройки, ведущиеся в отдаленных и небольших населенных пунктах и в сельских местах. Объясняется это тем, что производством цемента до сих пор занимаются только крупные промышленные предприятия и что он все еще является строго фондируемым материалом.
В современной цементной промышленности, базирующейся на специальном сырье, принята весьма громоздкая технология, нуждающаяся в огромных заводах со сложным и дорогостоящим оборудованием. В качестве сырья для таких заводов обязательно нужны огромные залежи так называемых естественных карбонатных пород, то есть мергелей, мела и других, которые имеются далеко не во всех районах страны. Кроме того, для получения цементного клинкера из такого сырья нужны специальные обжигательные печи длиною до 185 м, огромные склады с вместительными хранилищами бункерного типа для хранения сырья и готовой продукции, сложное дробильно-размольное и другое оборудование. Все это исключает возможность повсеместного производства цемента и резкого увеличения его выработки для наиболее полного удовлетворения нужд многочисленных строек. А между тем имеются все возможности для того, чтобы производство цемента сделать поистине массовым и повсеместно доступным.
ВСПОМНИМ ЗАБЫТОЕ
Забиваем Сайты В ТОП КУВАЛДОЙ - Уникальные возможности от SeoHammer
Каждая ссылка анализируется по трем пакетам оценки: SEO, Трафик и SMM.
SeoHammer делает продвижение сайта прозрачным и простым занятием.
Ссылки, вечные ссылки, статьи, упоминания, пресс-релизы - используйте по максимуму потенциал SeoHammer для продвижения вашего сайта.
Что умеет делать SeoHammer
— Продвижение в один клик, интеллектуальный подбор запросов, покупка самых лучших ссылок с высокой степенью качества у лучших бирж ссылок.
— Регулярная проверка качества ссылок по более чем 100 показателям и ежедневный пересчет показателей качества проекта.
— Все известные форматы ссылок: арендные ссылки, вечные ссылки, публикации (упоминания, мнения, отзывы, статьи, пресс-релизы).
— SeoHammer покажет, где рост или падение, а также запросы, на которые нужно обратить внимание.
SeoHammer еще предоставляет технологию Буст, она ускоряет продвижение в десятки раз,
а первые результаты появляются уже в течение первых 7 дней.
Зарегистрироваться и Начать продвижение
Еще в 1825 году наш соотечественник Егор Челиев взял патент на способ производства «мартеля», то есть цемента из гашеной извести и обыкновенной глины. Способ этот был основан на повторном обжиге извести в печах вместе с глиной, находящейся в брикетах. После спекания брикетов их дробили в ступах, а потом размалывали естественными каменными жерновами крепких пород в тонкий порошок, превращая таким образом брикеты в цемент.
Как видим, предложенная свыше ста тридцати лет тому назад Егором Челиевым технология изготовления цемента весьма проста и общедоступна. Но, к сожалению, она незаслуженно была забыта.
Спрашивается, почему?
Широко осуществленная Челиевым идея раздельного обжига извести и спекания клинкера не получила дальнейшего развития потому, что известь в этом случае применялась в гашеном виде. Это приводило к весьма медленному высыханию известково-глиняных брикетов в естественных условиях перед спеканием в клинкер. А также потому, что из-за отсутствия печной и дробильно-помольной техники клинкер толкли в специальных ступах с конными приводами.
Но сейчас совсем другое дело. Теперь, когда уже выявлены новые свойства негашеной извести и когда старая теория твердения ее уступила господство новой, так называемой «гидратационной теории», разработанной кандидатом технических наук Б. В. Осиным, появились новые возможности успешно возродить раздельную, легко доступную технологию производства цемента и осуществить ее на новой основе.
НАШИ ПРЕДЛОЖЕНИЯ
Около 30 лет тому назад мною были открыты новые свойства извести, а именно — ее гидратационное твердение. Это заставило коренным образом пересмотреть существовавшее веками представление об этих свойствах. Оно уже получило научное обоснование в трудах советских ученых и заложило основу новой теории производства вяжущих и самих строительных материалов.
Эта теория, а также опыт Челиева убедили многих в том, что проблему создания упрощенной технологии производства цемента можно решить только при разделении основных процессов получения цементного клинкера на две части. Первая часть процесса — обжиг известняка с целью получения из него комовой извести, и вторая часть — скоростное спекание в малогабаритных и весьма простых по устройству спекательных аппаратах шихты, приготовленной из смеси глины и негашеной извести.
По этой упрощенной технологии производства цемента в шихту вводится не известняк, а негашеная известь, так называемая «известь-кипелка», которая смешивается с глиной в дробильно-размольных аппаратах. Причем шихта состоит в среднем из 55% извести и 45% (в пересчете на сухое вещество) глины.
Полученная таким путем смесь прессуется в брикеты, окаменение и обезвоживание которых происходит весьма быстро за счет гидратационного твердения негашеной извести и разогревания от развиваемой при этом теплоты. Затем брикеты, в зависимости от плавкости глины, спекаются при температуре 1000—1100°, после чего дробятся и размалываются в шаровых мельницах. Полученный в результате размола порошок и есть тот цемент, который с успехом может быть применен для целей массового жилищного и производственного строительства, так как прочность его составляет в среднем 100 кг/см2, то есть соответствует обычному цементу марки «100».
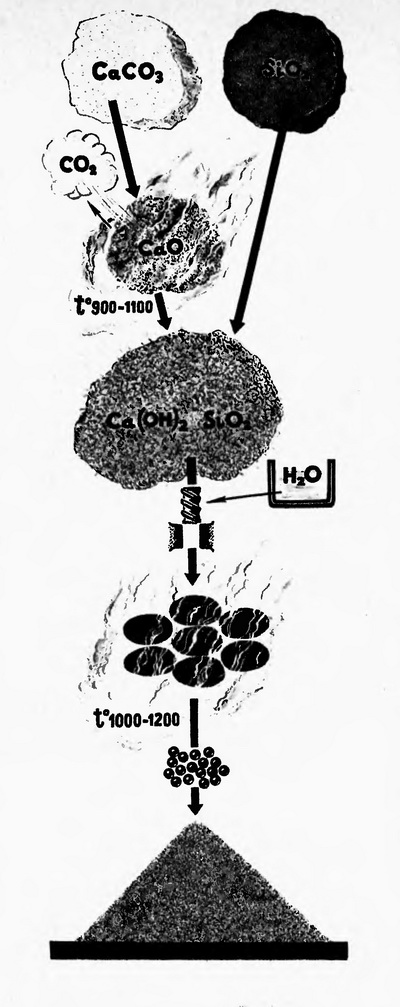
Сервис онлайн-записи на собственном Telegram-боте
Попробуйте сервис онлайн-записи VisitTime на основе вашего собственного Telegram-бота:
— Разгрузит мастера, специалиста или компанию;
— Позволит гибко управлять расписанием и загрузкой;
— Разошлет оповещения о новых услугах или акциях;
— Позволит принять оплату на карту/кошелек/счет;
— Позволит записываться на групповые и персональные посещения;
— Поможет получить от клиента отзывы о визите к вам;
— Включает в себя сервис чаевых.
Для новых пользователей первый месяц бесплатно.
Зарегистрироваться в сервисе
Принцип раздельной технологии получения цемента по упрощенной схеме уже успешно осуществлен на Карповском кирпичном заводе в городе Горьком и на Домодедовском известковом заводе под Москвой. Это говорит о том, что к производству такого цемента можно приступить немедленно там, где уже есть либо известковые, либо кирпичные заводы. А там, где их нет, можно организовать новые цементные предприятия, для оснащения которых требуется весьма несложное, выпускаемое нашей промышленностью в массовом порядке дробильно-размольное оборудование и очень простые печи. Таким образом, производство цемента становится общедоступным и позволяет широко использовать местное сырье, то есть известняк и глину, которое имеется почти всюду.
ПРИНЦИПИАЛЬНАЯ СХЕМА
Процесс производства цемента разделяется на две части: на термохимическую и механическую. К первой из них относится получение из исходных материалов — известняка и глины — цементного клинкера, а ко второй — дробление и помол этого клинкера.
Нет необходимости подробно описывать процесс обжига камня-известняка и получение из него комовой извести — он давно и хорошо всем известен. Дробление негашеной извести также может производиться на существующих известковых заводах и на том же оборудовании. Менее известным является упрощенный процесс получения цементного клинкера. Поэтому мы и остановимся на нем более подробно.
Исходными компонентами для составления клинкерной шихты являются комовая известь-кипелка и обыкновенная глина, взятая прямо из карьера. Причем известь необходимо предварительно измельчить бегунами в крупку.
Затем дробленая известь-кипелка и разрыхленная карьерная глина естественной влажности через тарельчатые дозаторы поступает в сырьевую шаровую мельницу, где известь начинает гидратироваться, то есть гаситься. При этом она отнимает воду из глины, благодаря чему вся перемалываемая масса сильно разогревается за счет экзотермического процесса, происходящего при гидратации извести с водой. В мельнице происходит сложная термохимическая реакция, в результате которой смесь бурно кипит, причем образуется тонкодисперсная масса,
которая и поступает в горячем виде в обычный шнековый пресс для брикетирования.
В ходе технологического потока изготовления брикетов они затвердевают и даже высушиваются, что происходит благодаря наличию в смеси извести с глиной большого количества тепла. Полученные таким образом брикеты в затвердевшем и высушенном виде сразу же поступают в зону высоких температур — на спекательную решетку, в вагранку или в любую другую печь, где они спекаются, оплавляются или даже доводятся до расплава, в результате чего и образуется цементный клинкер.
Ввиду того что в полученных брикетах не содержится углекислоты, процесс спекания резко сокращается. Причем для этого не нужно длинных печей специальных и сложных конструкций. Весь процесс спекания шихты в цементный клинкер может осуществляться в малогабаритных печах, на агломерационных решетках, на установках для получения керамзита, а также в широко распространенных тоннельных, кольцевых, шахтных и других печах. Короче говоря, спекание клинкера можно осуществить в любой печи, даже в напольной, при расходе топлива, не превышающем установленных норм для известковой промышленности. При этом вес шихты на одну тонну цементного клинкера составляет всего лишь 1 120 кг.
Завершающая стадия получения цемента — помол полученного клинкера — также может осуществляться с помощью любых существующих агрегатов для измельчения.
Принципиальная схема производства цемента по новой технологии показана на второй странице обложки, а схема физико-химического процесса превращения извести и глины в клинкерный цемент — на приведенном здесь рисунке.
Описанная технология производства цемента из местных материалов значительно расширяет возможность получения цемента марок «200» и «250» и делает доступным производство такого материала повсеместно, не прибегая к сооружению крупных индустриальных заводов. А что это значит для всемерного развития строительства — об этом говорить излишне!
Техника молодёжи 1957 год
|